Case Study: Modular Removable Rotary Dryer Insulation
Rotary Dryer Insulation in Missouri
When a major food and pet care manufacturer first opened their new facility in southeast Missouri in 2021, they were faced with sustainability goals set by the corporation that what felt like a monumental challenge. Meeting these goals meant attempting to insulate their rotary dryer. This was difficult for many reasons, including that the rotary dryer:
- Is an enormous piece of constantly moving equipment
- Is located outdoors
- Does not have a uniform surface temperature,
- Includes several protruding pieces that needed to be accounted for
when installing insulation.

A first-of-its-kind modular, removable, rotary dryer insulation solution |
Project Overview: Industrial Dryer Insulation
Thermaxx’s Alex Unger went on site to take detailed photos of the equipment that corresponded to drawings provided by the manufacturer. They then leveraged their in-house expertise and technology to develop a first of its kind custom modular removable, serviceable, and reusable insulation jacket.
This innovative approach made the installation process quick and relatively painless for the facility, as it was completed over a weekend using only a boom lift. The modular design also makes servicing the dryer easy, as only small parts of the entire insulation jacket need to be removed to access the dryer. Additionally, putting the insulation back on is using a combination of hook and loop (i.e., Velcro®), straps, and D-rings.
The Thermaxx Difference
- Expert field team and mechanical insulation designers that use a unique combination of knowledge, technology, and artistry to create custom solutions that meet their customers specific needs
- Top quality materials suited to specific use case including exposure to UV and moisture as well as hygiene concerns
- Production process that is ISO 9001:2015 certified
- An industry leading 5-year warranty on all installed products
- They make it easy for you, turnkey service includes project management of installation, leaving you and your team with bandwidth to continue to do your best work
- Minimal impact to production, 90% of install was completed in a single weekend
Project Highlights |
|
Components Insulated | Rotary Dryer |
Annual Energy Savings |
400,000 Therms 40,000 mmBTUs |
Solutions |
Removable panels |
Hot Side Materials | Vermiculite/Fiberglass, silicone |
Cold Side Materials | Silicone fiberglass |
ROI | 20 Months |
Need help with your unique insulation or energy savings project? We’re here to meet your Midwest facility’s needs. For more information on how you can begin saving time, money, and energy in your facility with innovative Thermaxx solutions, contact us. You can also download a PDF of the case study here.
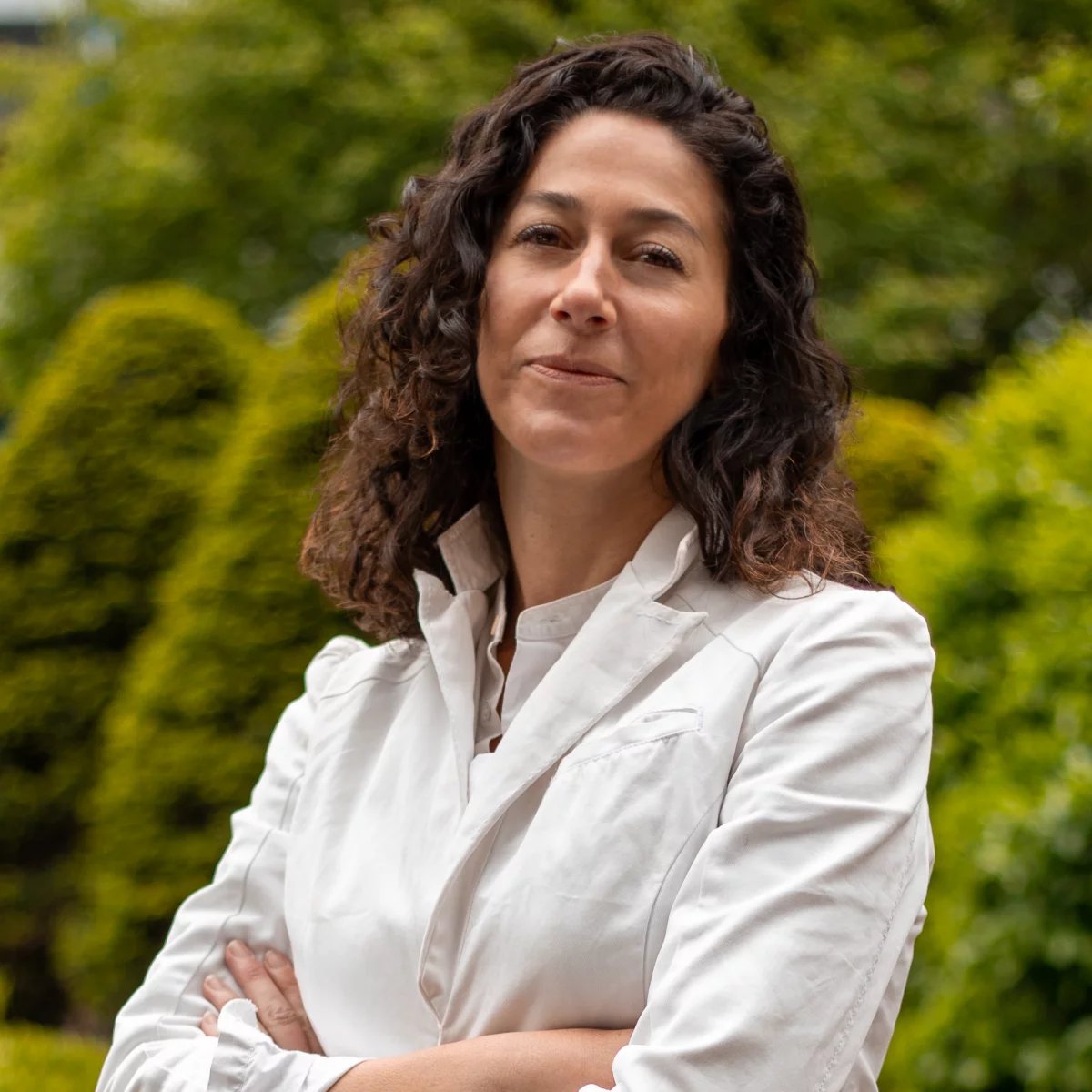
Rose Titcomb - Account Manager at Thermaxx
Rose Titcomb comes to Thermaxx as our Northwest 2018 sales partner. Having grown up in the city by the Bay, San Francisco, she understands the importance of community. That community feeling has driven her to play team sports and run a business for half her career. She has ties to the East Coast from the mom and pop store her grandfather owned in upstate New York to her schooling days. She is excited to embrace a new venture she believes is a valuable tool for many businesses with the Thermaxx family and looks forward to the new relationships she will make. In her free time Rose loves’ #1 loves are her children. You may also catch her hitting the ball around and eating her way thru the windy city by the Bay.
Categories
- removable insulation
- thermaxx jackets
- energy savings
- savings
- energy efficiency
- safety
- pipe insulation
- energy
- case study
- insulation materials
- thermal insulation
- heat loss survey
- heat loss
- energy loss
- hot insulation
- fiberglass
- installation
- steam
- New York
- custom insulation
- NYC Case Study
- boiler
- university
- Connecticut
- reusable insulation